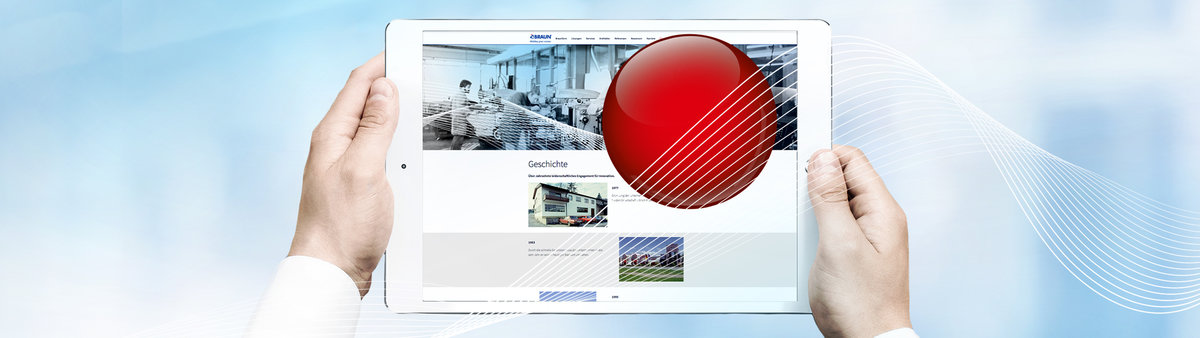
Braunform as exhibitor at K 2022
In focus: the patented RotaricE²® solution
12.08.2022
At this year's K 2022, the leading international plastics trade fair from October 19 to 26, 2022 in Düsseldorf, Germany, Braunform will present its patented innovation RotaricE²® for compact integration solutions demonstrated by a mold for a Luer connector (closure cap pharma).
The RotaricE²® technology is a clever combination of 2-component, servo technology and final assembly of the component in a very limited space. The focus is on reducing costs under the TCO (Total Cost of Ownership) approach while increasing production efficiency. By means of the translational closure of caps in the mold, it is possible to positively influence all production factors. And not only that, with RotaricE²® Braunform also provides a sustainable mold concept that ensures production via process control instead of quality control. The project was realized together with the partners Arburg GmbH + Co KG, Ewikon Heißkanalsysteme GmbH, Agathon Deutschland GmbH, iQtemp GmbH, Kistler Instrumente GmbH, Meusburger Georg GmbH & Co. KG, Oerlikon Balzers Coating Germany GmbH and Uddeholm.
Resource-saving and cost-effective. Now what exactly does RotaricE²® mean? In very concrete terms, RotaricE²® resulted in savings of over 45% in the production process. However, the technology not only saves time and money, it also above all eliminates the need for two injection molds and machines, as well as an assembly line for assembling the individual parts, including the production floor. For the purpose of achieving, for example, capping in a multi-component application in just one work step in a very limited space, Braunform developed the redirection of a rotary movement into a translational movement within a mold. The integrated servo-electric, rotary drives move in the mold quickly, gently and with wear detection. This solution is particularly advantageous because it enables an enormously compact radial arrangement of mold cavities with slides or masking devices around a sprue or preferably a sidegate system. This results in a reduction in cost and resource consumption and at the same time a benefit in terms of integrative vertical production depth in just one mold.
Mold for a 2-component Luer Connector with all-in-one functions. During the entire exhibition period, an example of this mold principle will be showcased at the Arburg booth in Hall 13 Booth A13. On an Allrounder More, the 2C article with small dimensions will be produced with a diameter of 10 mm and a length of 11 mm. The special feature of the mold is the combination of the capping function and the unscrewing function of the Luer-Lock thread in one multi-component sidegate mold.
The compact design allows a high number of cavities at small mold size. Therefore, the 4+4-cavity mold at the trade show serves as the basis for a compact series mold in modular design of up to 64+64-cavities.
An extraordinary challenge is the small shot weight of the 2nd component: With 0.05 g of the TPE component, the injection unit as well as the hot runner system from Ewikon must be designed very precisely.
During the development of the mold, special attention was paid to the modular design, i.e. the modules are individually centered and easily accessible.
A further benefit: the cleanroom-compatible design of the mold. The Braunform MED Mold® concept, well-proven since 2010, stands for the safe use of injection molds in cleanrooms. In addition to electric drives and corrosion-resistant steels, low-fat lubrication using coatings from Oerlikon Balzers and rolling element centering systems of Agathon ensure a reliable cleanroom operation. Furthermore, diffusion-welded inserts from IQtemp ensure close-contour cooling of the die inserts on the nozzle side.
No less than six functions are integrated into the ejector side in the smallest possible space: In detail, these are the core-back function, two sliders per cavity, lifting of the lid by means of a lifter, translational capping of the closures, unscrewing and final ejection. The 2nd component is formed by means of the core-back system, which means that no repositioning of the item is required. Sliders, which are actuated by pull/push parts when the mold is opened, demold the snap-on hooks for the lid. A lifter lifts the lid out of the mold cavity so that the closure can then be capped while still in the mold using the patented in-mold capping system. As final step the Luer thread is molded and demolded by a thin unscrewing sleeve. The final demolding of the assembled product is performed by a thin pipe ejector with a wall thickness of 0.60 mm. The four main movements core-back, lifter, in-mold capping and unscrewing are controlled by AMK servo motors. Ejection takes place via the machine ejector.
Process control instead of quality control. Process monitoring takes place by means of two indirect pressure sensors per mold cavity developed by Kistler, i.e. defective parts are detected and sorted out by the handling system. To implement the complete project, the hot runner specialist Ewikon equipped the hot side with a Smart-Control system to ensure permanent data analysis as well as data evaluation (real-time data mining). Also involved in the realization of the mold was the moldmaking partner Meusburger. It was on the standby for the supply of plates and high-quality standard parts.
With the trend-setting RotaricE²® mold concept, the moldmaking specialist presents a technologically innovative and creative approach to resource-efficient production by integrating several production steps into one single mold concept. The engineers at Braunform know that future production will require even better and more sensible technology in order to produce in an efficient and sustainable manner. The ideal combination of 2C, the use of servo technology and final component assembly in a very small space enables new production concepts with lower space requirement and investment volume. In this way, product functions from several individual parts can be combined into a 1-part article.
Braunform at the fair K 2022: Hall 1, Booth C26
Contact Person
Marketing
Tel. +49 (0) 7663-9320-0
marketing@braunform.com